May 11, 2023
How Agritecture Helps Our Clients Make More Informed Decisions As Automation Reshapes the Indoor Farming Industry
Written by: Ricky Stephens and David Ceaser.
May 11, 2023
It’s no secret that automation is transforming every sector of the economy. With the cost of labor increasing dramatically in recent years, combined with meaningful improvements in technology development, cost-benefit analyses are increasingly tilting in the favor of automation.
Let’s consider a hypothetical example, where the cost of an automated crop harvesting machine decreases by 6% every year due to technology advances, economies of scale, increased competition, or any other number of factors. Meanwhile, the cost of labor is increasing by 8% each year. Doesn’t seem like too meaningful of a difference year-to-year, right?
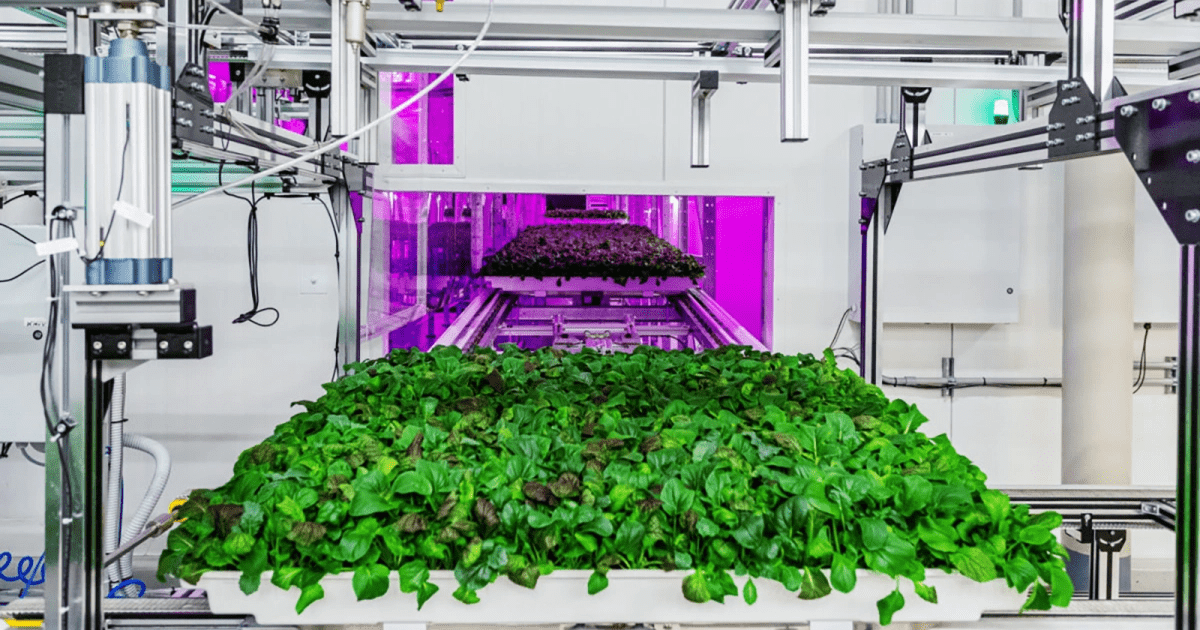
Credit: Free Think.
Well, let’s do the math.
Just five years ago, in 2018, let’s say the crop harvesting machine cost $1,000,000 for a grower to purchase. And let’s assume that machine could perform the same amount of harvesting work as 3 laborers who are paid $12 per hour. With another 15% in taxes and benefits, each laborer costs the company $27,600 per year. Is it worth it to purchase the equipment and replace the workers? From a purely financial standpoint, probably not: the payback period is 12 years, and that doesn’t even take into consideration any maintenance or depreciation of the equipment.
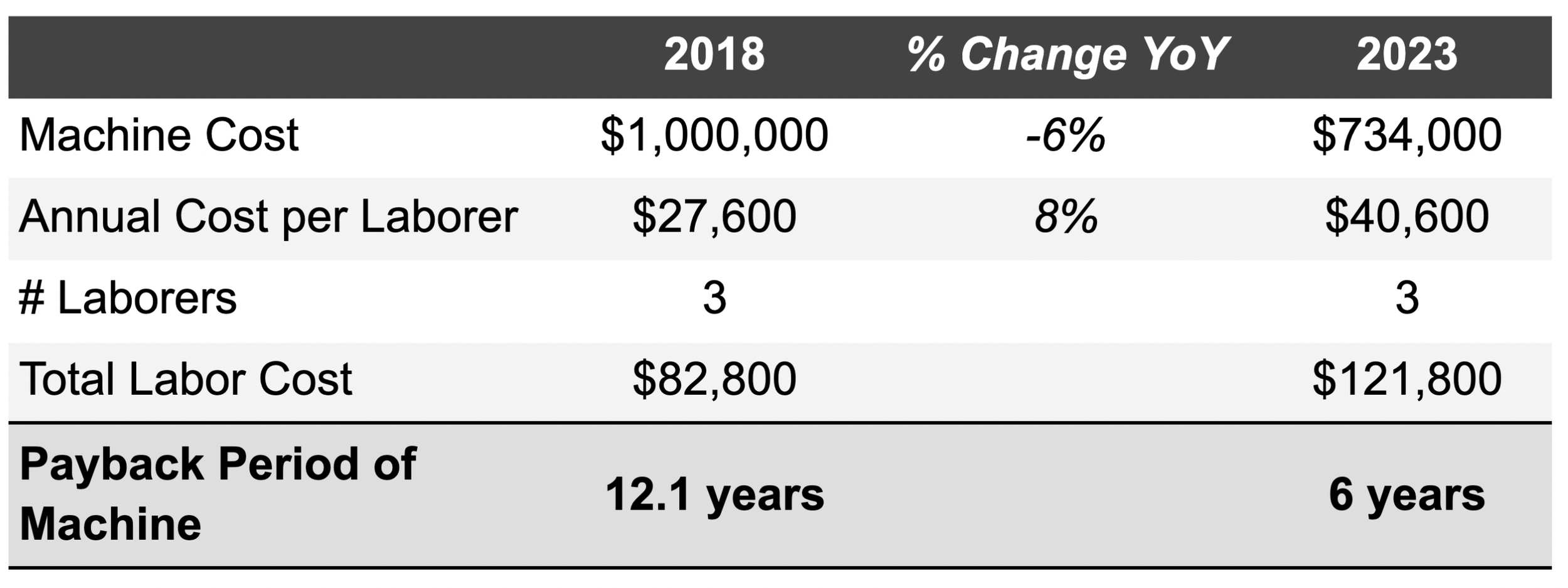
But today, in 2023, that same machine would now cost the company $734,000. Meanwhile, those employees are now earning more than $17 per hour. Suddenly, the return on investment (ROI) equation looks very different: the payback period has been cut in half, down to 6 years!
Now, of course, we’re not taking into account other factors including the cost of a loan which may be necessary to purchase the equipment - but the point should be clear.
How This Plays Out in the Real World
This type of equation is being run in offices (and on farms!) around the world. And not only is the payback period looking better and better on paper, but when factoring in the challenge of attracting and retaining a workforce that so many companies have been struggling with since the pandemic, choosing automation may help companies feel more stable and resilient to future threats.
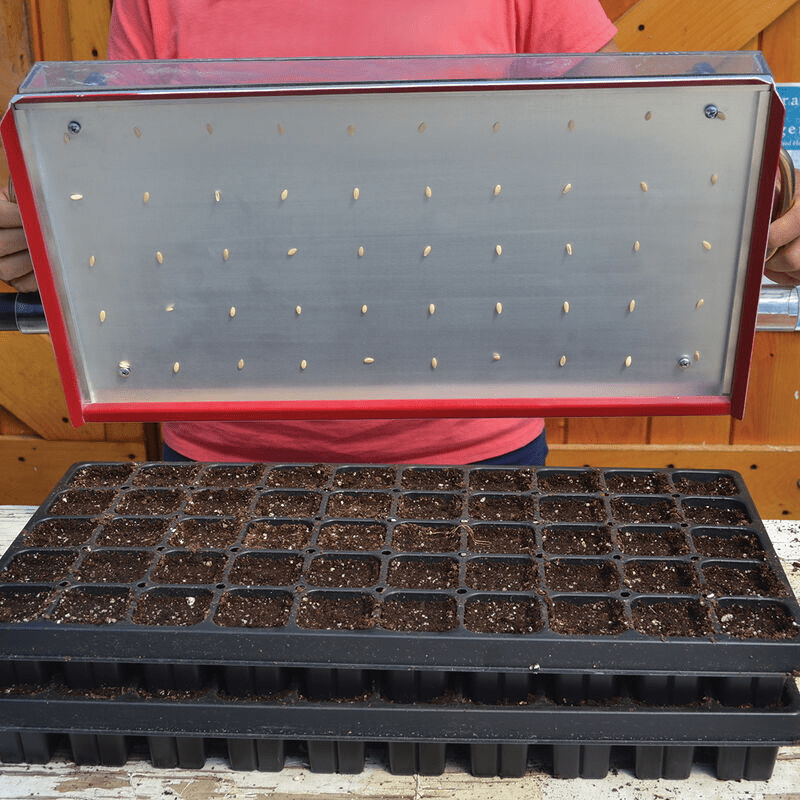
Credit: Johnny’s Selected Seeds.
One challenge with automation, however, is that there is typically a major economies of scale component to the equation. Because if a large piece of automated equipment can replace dozens of laborers, but your farm only employs five people, the ROI won’t make sense. This is why we see a general trend of large-scale facilities investing the most in automation, while smaller-scale facilities rely more heavily on manual labor.
Yet automation doesn’t only look like robots picking tomatoes utilizing the most advanced machine vision and AI technology. There is a wide spectrum of tools that can be classified as automation, and the bottom line is that these tools help increase overall worker efficiency. Automation tools can be as simple as a vacuum seeder which significantly increases task efficiency, but still needs to be performed by a human.
At Agritecture, we talk to CEA entrepreneurs and project developers looking at options across the automation spectrum who want to make sure they’re properly weighing their available options and making the smartest decision for their crop, farm and business model.
With hundreds of suppliers out there, many of whom are a bit mysterious as to pricing and equipment performance, this can be a daunting task.
Here’s how Agritecture can help you.
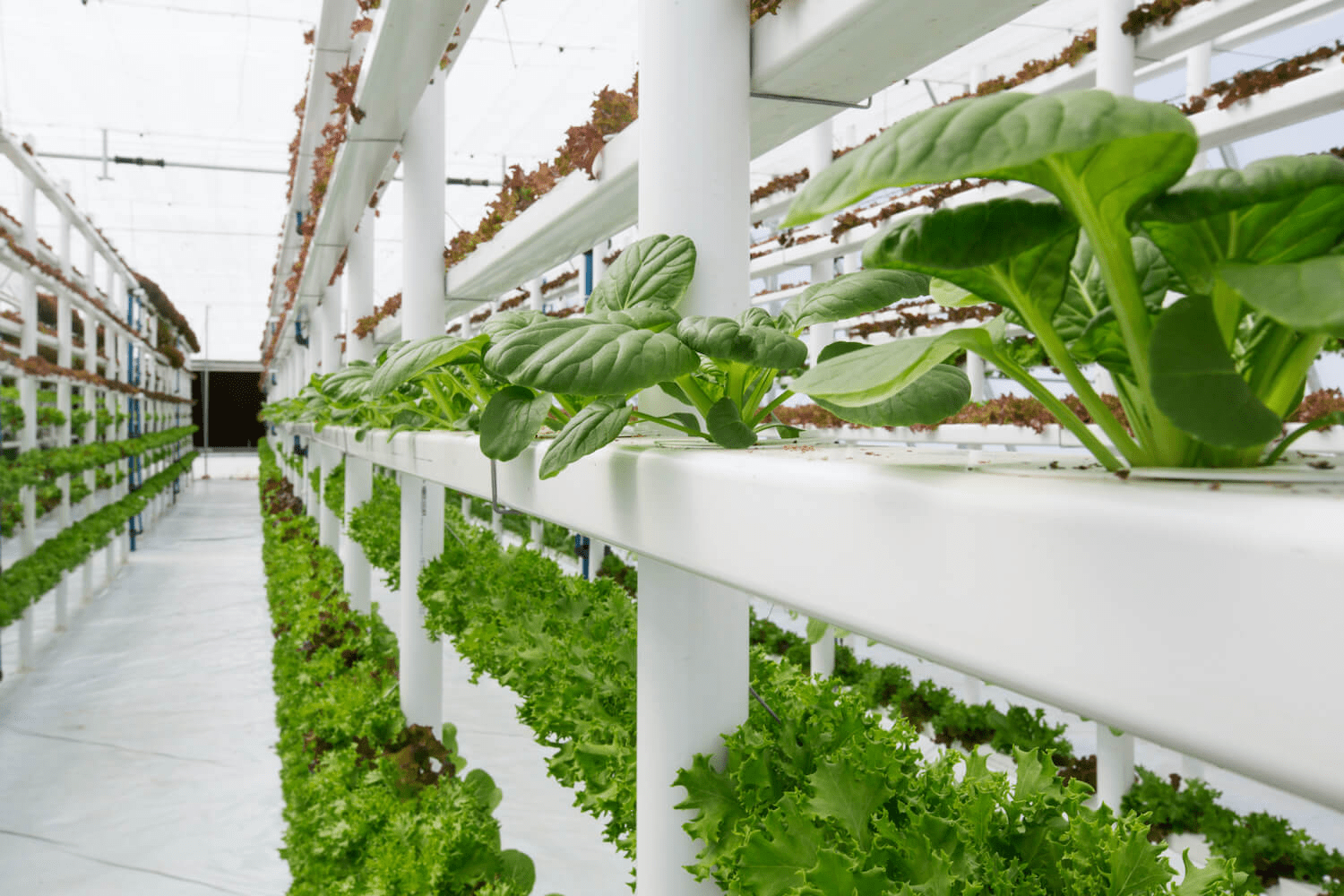
Credit: The Counter.
Using Agritecture Designer’s farm modeling tool, our users can already run financial estimates for any type of greenhouse or vertical farm. And now, as part of the platform’s latest series of updates, we have added the ability for users to play with different levels of automation when modeling their farm. Users can simply choose from preset levels of low, medium, or high automation, and our software will determine the best type of equipment and corresponding labor requirement by job function. The algorithm that determines these selections is based on intensive research we performed earlier this year on various automation solutions for farms of many sizes and crop types.
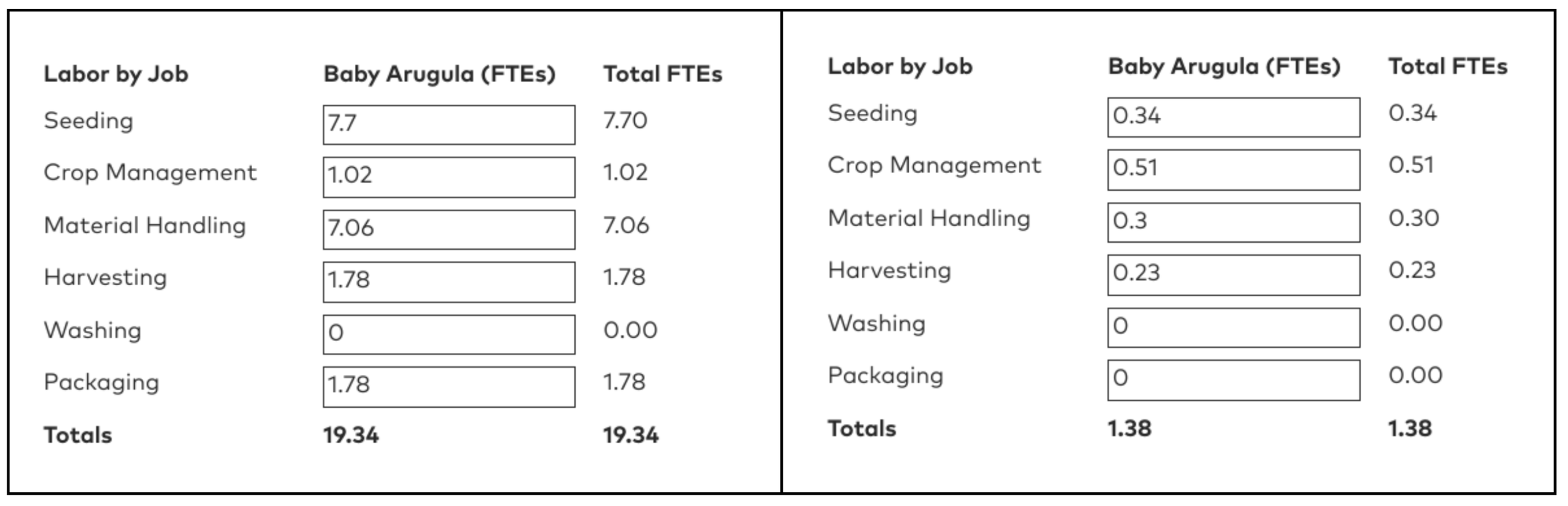
Let’s review a specific example of a vertical farm growing baby arugula, producing about 10,000 lbs per month. The image on the left estimates the total labor count of the low-automation scenario at 19.3 FTE (full-time equivalents), whereas the high-automation vertical farm in the right image estimates a total labor count of just 1.4 FTE. Of course, the latter scenario has a much higher CapEx given the increased investment in automation.
What Comes Next?
Given where the CEA industry is heading, we believe these updates will be critical for anyone looking to model real-world scenarios of greenhouses and vertical farms and weigh the CapEx-OpEx tradeoffs of investing in automation. But we’re not stopping here. Soon, you’ll have the ability to choose not just between low / medium / high levels of automation, but also between specific pieces of equipment (such as seeding or harvesting equipment), and in both scenarios to see the corresponding effect on labor costs. We’ll also continue working closely with new and existing members of our Partner Network to ensure these estimates are tied to real-world performance data.