Sep 7, 2022
Here’s Why Architects and Farm Planners Love Working With Montel
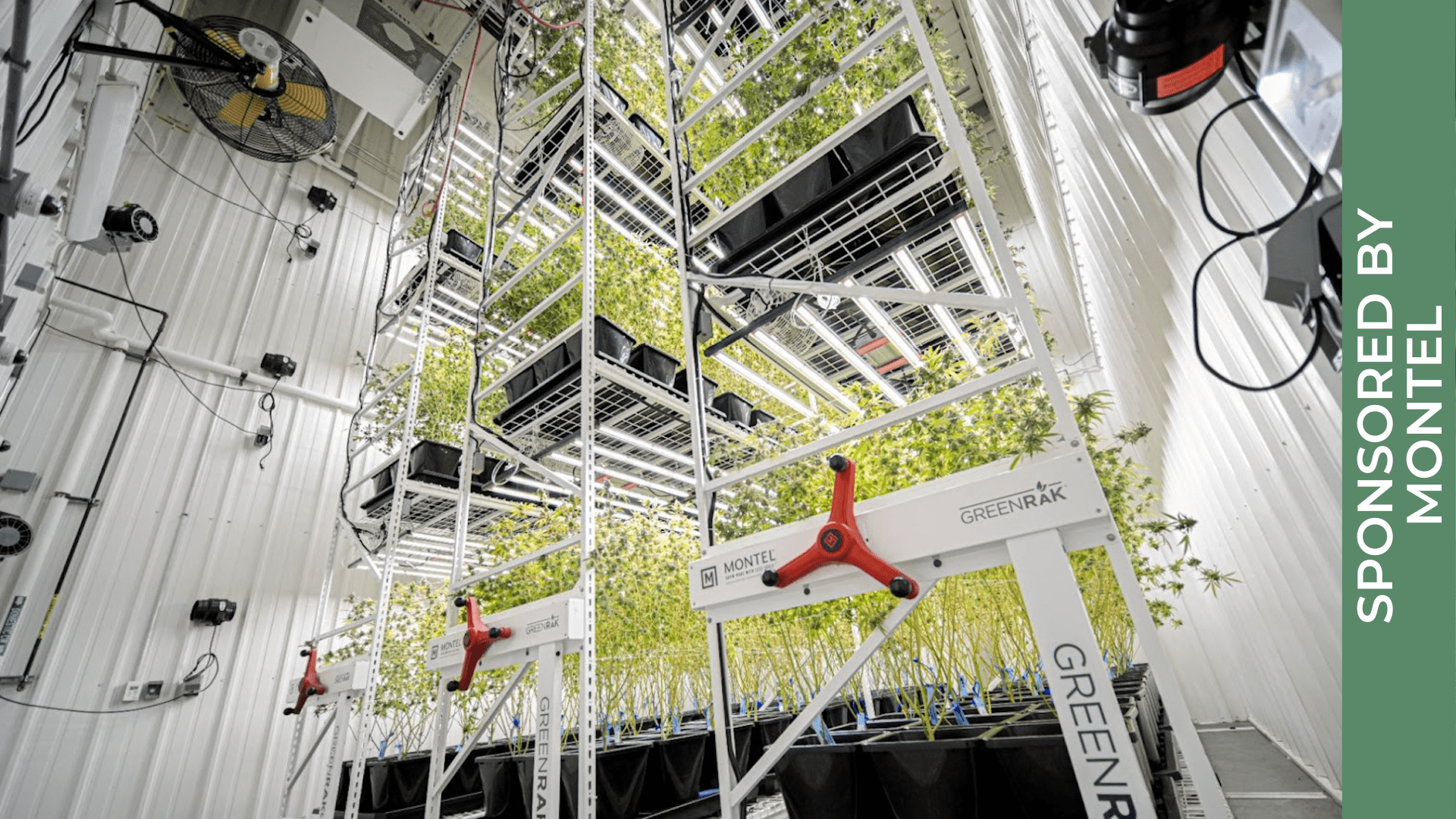
Written by: Sarah Jordan
In vertical farming and CEA facility development, the ability to maximize one’s physical footprint is of utmost importance. Mobile racking solutions allow farms to do more with less space, saving money and increasing yield per square foot. This fact has now been well-documented due to leading racking solution providers like Montel. However, less attention has been given to factors beyond yield and savings– factors including ongoing maintenance costs, product longevity, market history, and safety standards.
When it comes to CEA facility planning, these are the types of factors that architects are more privy to. Whereas entrepreneurs tend to look for cost-saving measures, architects often think more deeply, and from a more technical lens, about the products they select or recommend for indoor farms.
TJ Davis is a sales consultant at Workspace Technology, an authorized Montel dealer, who has worked with several architects on indoor farming projects. He has also collaborated with Montel to install and service their racking solutions for multiple vertical farming facilities, including a lettuce farm in Orlando and a medical cannabis facility in Tampa.

“Architects tend to want to understand every detail related to product specifications,” says Davis, emphasizing the care with which they recommend equipment when designing a CEA facility. They need to have a holistic view of the space they’re developing and balance the functionality of the space with practical details like meeting code requirements.
Architects and farm planners are likely to choose and stick with Montel because of their high-quality manufacturing standards. They build products to last, and through research and development, they have made their products rust-resistant in various materials, such as stainless steel, galvanized steel, or aluminum. Even with high-quality products, maintenance is eventually needed for products that receive heavy daily use. That’s why Montel has also made it very easy to swap out parts such as chains or handles, a service that Workspace Technology specializes in.
Montel has a long history in the market, and their success is due to various factors. Adam Sitterly, an architect with Anderson Porter Design, has worked with Montel on several CEA projects. He believes that one reason why Montel provides a great customer experience is their extensive market history, and therefore their ability to bring partners to existing facilities that utilize Montel’s products.
Sitterly believes that “there’s no substitute for seeing the product inside a facility,” referencing the ability to view the racking in use with other key components of the farm, such as fertigation lines, fans, lights, trays, and fire suppression systems. “It’s invaluable to observe the orchestration first-hand.”

Still, a close second for Sitterly and other architects is the ability to visualize and map out a certain product within a 3D building render through modeling software such as Autodesk Revit— so it is quite helpful that Montel’s products can be found in the Revit library as well.
Montel’s experience in the industry is one of the main factors that helps them to achieve their goals with clients. Montel has produced mobile storage systems for educational and artistic institutions since 1924, and over time graduated into new verticals and innovated with new product lines, including mobile racking for indoor farms. With almost a century of experience, they have seen nearly any issue clients may throw their way.
This experience is valuable when seeking solutions to complex problems and allows them to work with experienced installers. According to JoAnne Dougall, Montel’s Director of Customer Service and Projects, “The quality of the installation is essential to optimal use and is a contributing factor to the longevity of a high-density mobile system.”
Montel’s distributor network is a great way to ensure proper installation. This group is comprised of authorized Montel dealers, who Dougall describes as “more than clients; they are Montel business partners.” They keep an open line of communication with these dealers throughout the installation process and beyond. By maintaining relationships with their partners, they can streamline installation and provide a meaningful experience throughout the customer's lifetime.
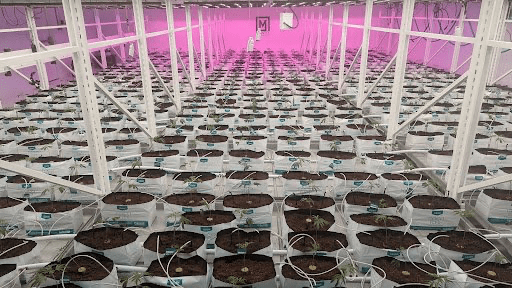
Workspace Technology is a member of this authorized dealer network, having partnered with Montel for around ten years. The partnership helps ensure efficiency, with Montel leading the design process and Workspace Technology installing and servicing systems.
Workspace Technology and Montel also collaborate to offer continuing education courses for architects, allowing these professionals the opportunity to better understand the integration of various racking solutions. The support that Montel can offer before, during, and after installation allows architects to have more confidence in their decision.
Building a vertical farm or CEA facility can be a daunting task. Working with experienced equipment and service providers is a proven path to success. Having been in business for nearly 100 years, Montel’s racking solutions are tried and true. Over time, innovations in technology have solved problems that they could not have imagined a century ago, and in our modern world, this level of experience is a huge asset to architects and planners working to build a better future.