May 2, 2022
An Entrepreneur’s 9-Step Guide To CEA Facility Design
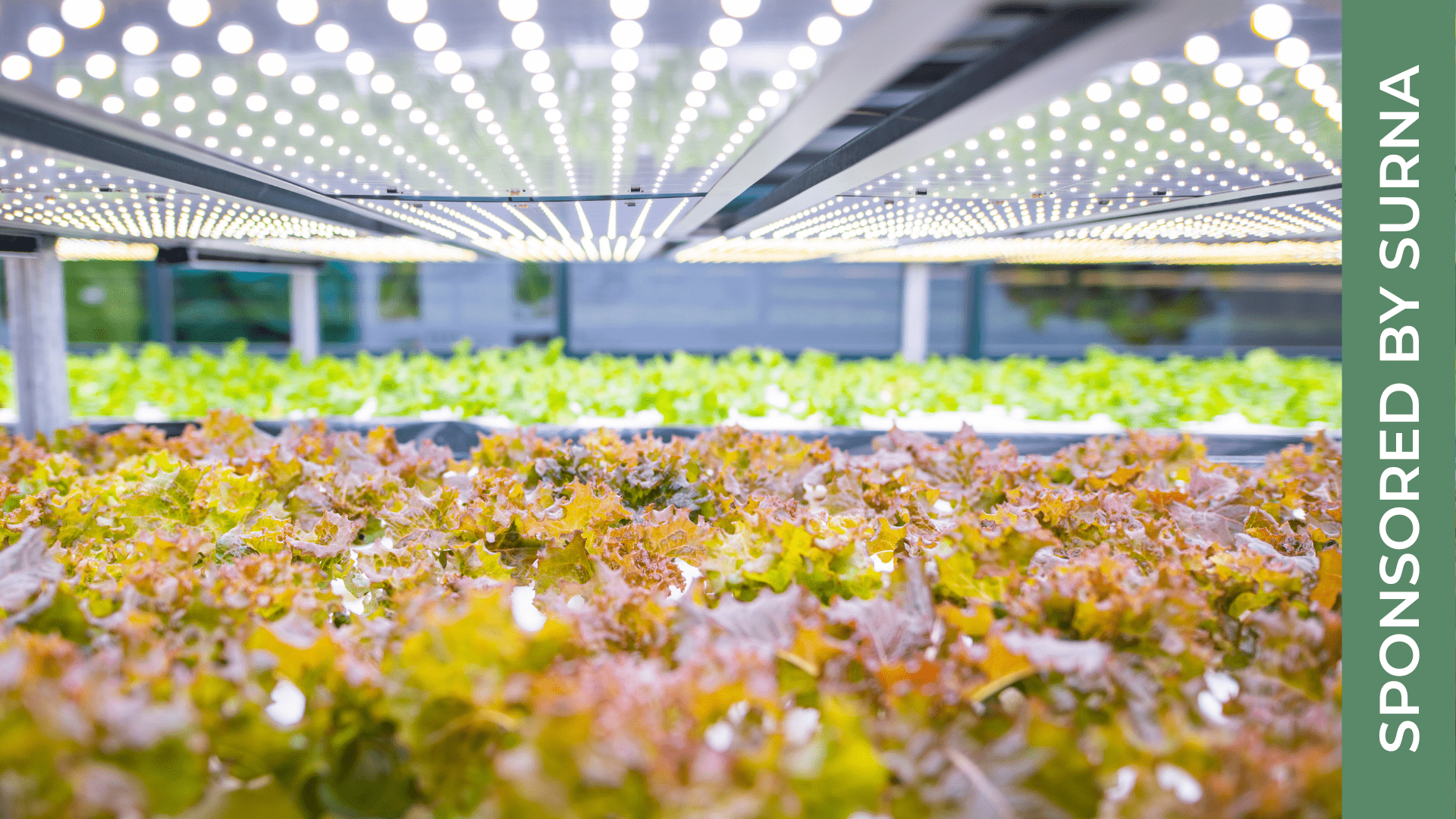
Editor’s note: Agritecture will be publishing more content about facility design in partnership with Surna Cultivation Technologies. Read the first blog post on how to make it or break it with your HVAC systems and watch the follow-up webinar on designing your CEA facility.
A lofty vision of re-localizing food systems, combined with the booming growth of the controlled environment agriculture (CEA) industry, has attracted many entrepreneurs to indoor farming. However, new entrants face a steep learning curve when it comes to the planning, designing, and construction of a farming operation built for success.
Agritecture meets tons of entrepreneurs with strong business skills or technology prowess, but they often lack the technical knowledge on commercial construction, biological systems or food safety to plan their operations effectively - or vice versa - those with technical expertise who are missing the business piece. The complexity of launching a business and building out a food-producing facility that is highly efficient, consistent, and safe is precisely why indoor farming poses so many unique startup challenges.
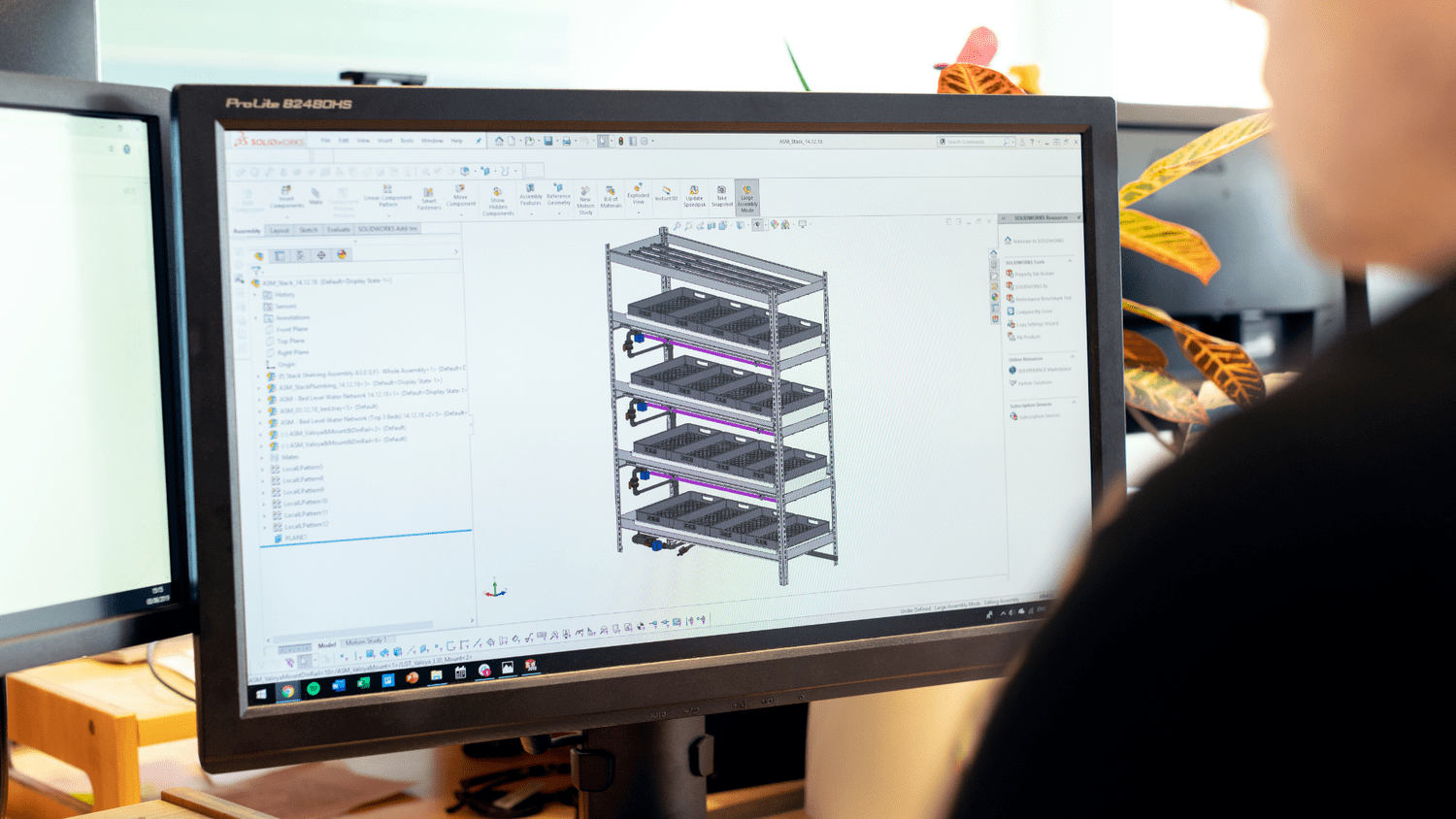
Farm planning expert Agritecture and facility design expert Surna Cultivation Technologies approach facility design in three main phases: pre-planning, design and operations.
Having served over 800 cultivators, with over 200 of them being large, commercial projects, Surna has a deep understanding of the key facility elements that foster a successful indoor grow. According to Surna, this experience in cultivation facility design, construction, climate management and facility operation allows them to help cultivators meet their goals by analyzing options for their facility, engineering carefully curated cultivation technologies into holistically-designed solutions, and providing the chosen technologies that maximize their success.
“Since I began tracking CEA operations over 10 years ago, one thing is certain and has remained constant - without proper research and planning, farms inevitably make costly mistakes that could have been avoided and too often fail. ”
“We suggest that before any major construction process begins, CEA entrepreneurs consider budget first. But really, the first step is finding the right team and expert partner to help you make your vision a reality. ”
Disclaimer: Agritecture and Surna recognize that facility design is not always a linear process and want to acknowledge that the order of the following steps may change based on each unique project circumstance. Financing is also a critical part of this process, often falling between pre-planning and design, but for the purposes of simplicity and focus, we have excluded it from this article.
It's crucial that, as an entrepreneur, you explore different options for your business. Successful pre-planning ensures that you “know before you grow” and that you're well-prepared to act on unexpected challenges.
Pre-planning involves everything that will be done to help formulate a solid business plan, which will inform steps further down the road in the design phase. Pre-planning includes concept development, market research, site selection, and economic analysis.
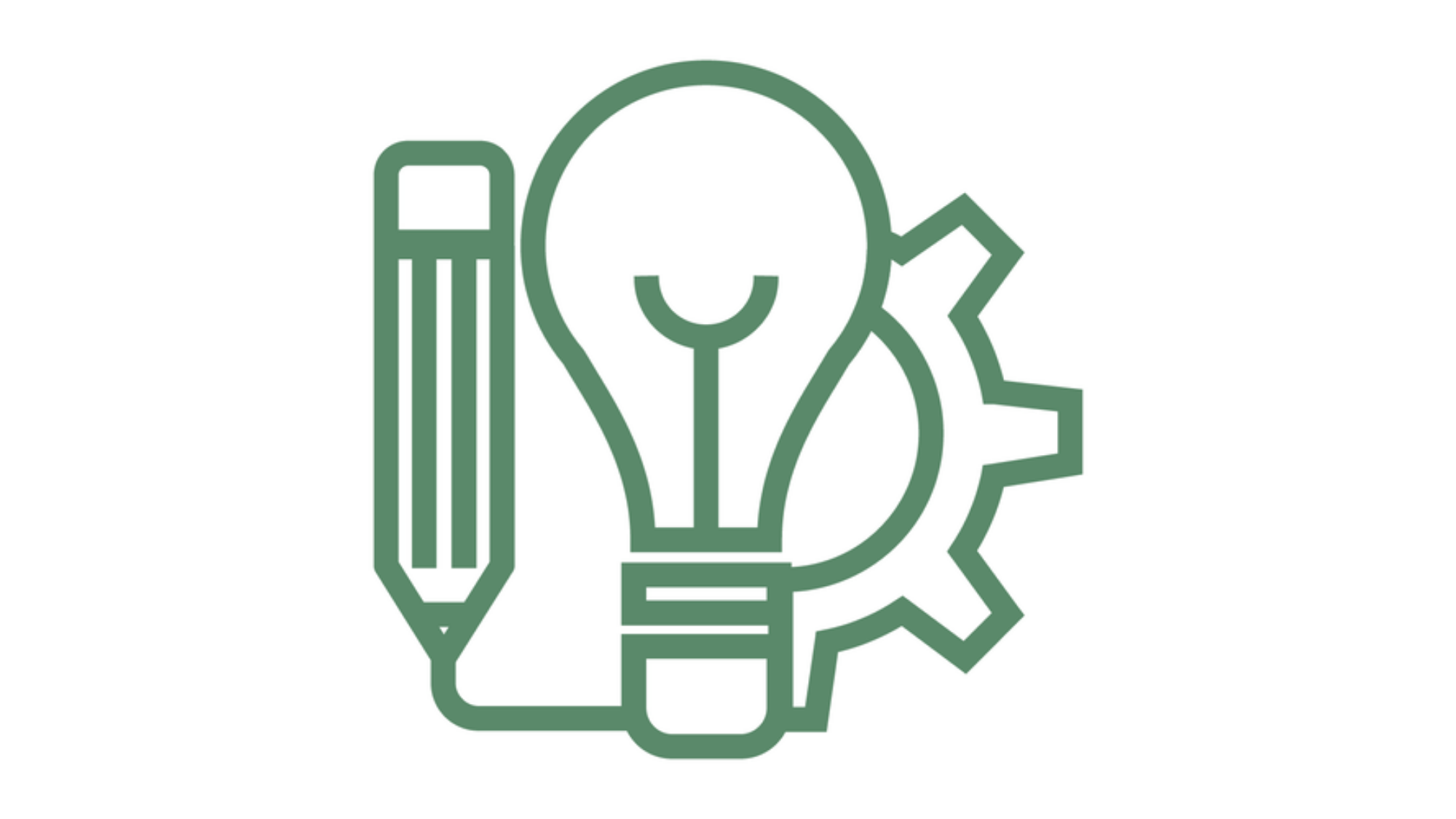
#1: Concept Development
This stage involves taking your exciting ideas and narrowing your scope: developing a viable farming concept by analyzing objectives, factors for success, stakeholders, and the regional agricultural landscape, while also setting a budget for your farm.
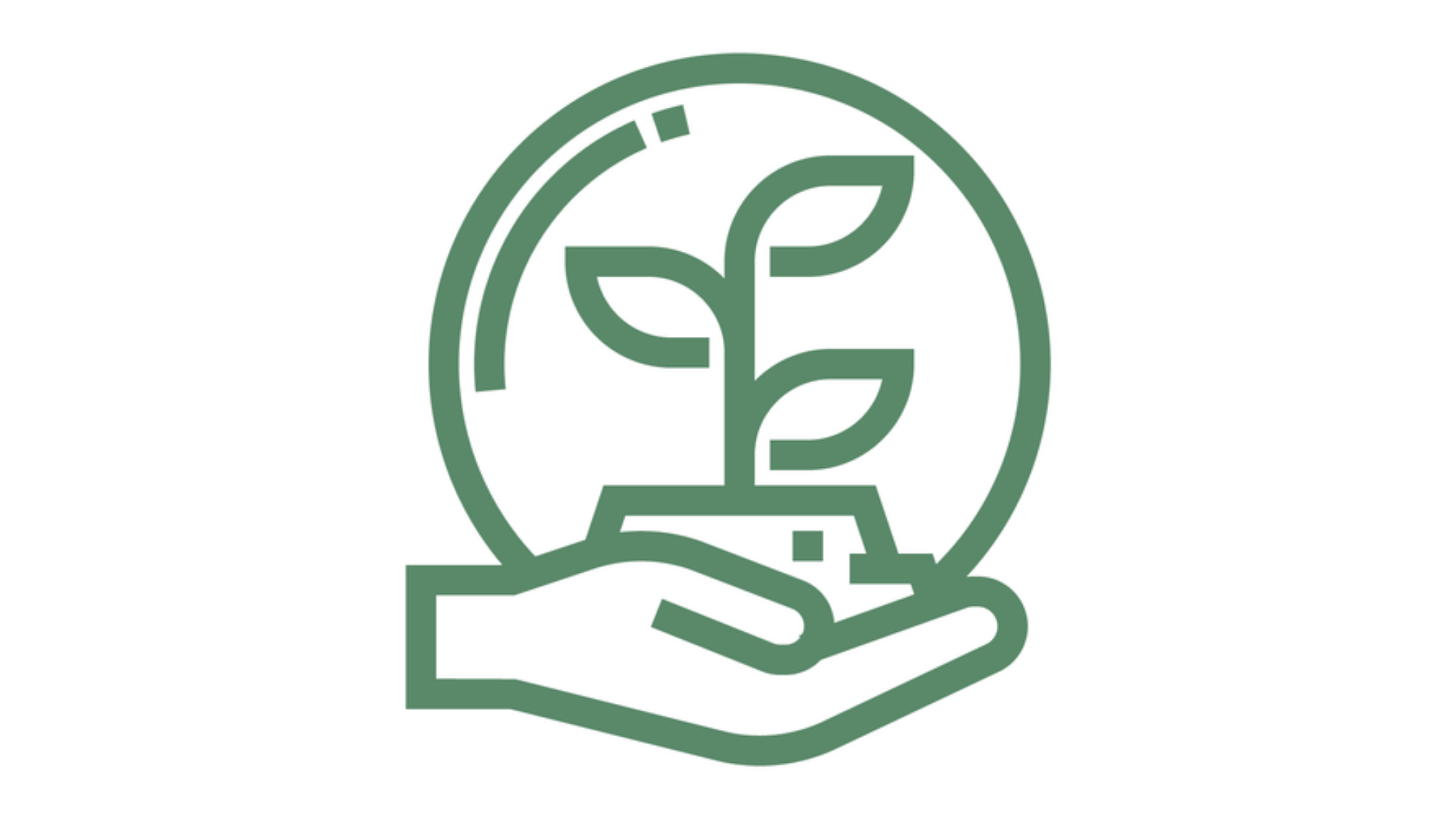
#2: Market Research
In this stage, you’ll need to better understand the gaps and opportunities in the local and regional markets. This step involves analyzing consumer and retail trends, selecting the crop(s) that will be grown, and devising a sales and distribution strategy.
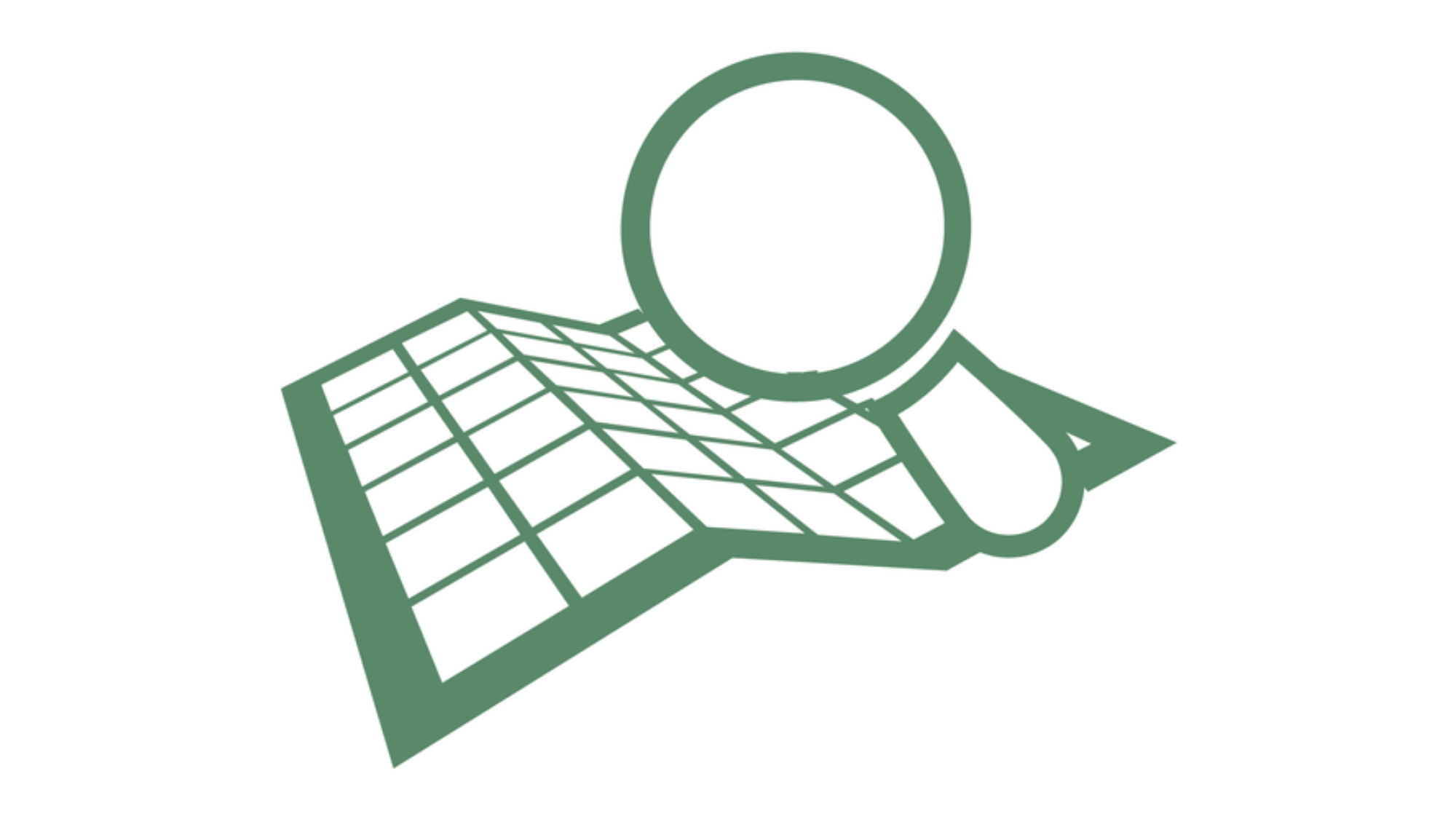
#3: Site Selection
In this stage, you'll need to decide whether to move into an existing site and retrofit it or build from scratch. Each comes with pros and cons, but some key considerations will include:
• Zoning codes
• Power and water infrastructure
• Wastewater regulations
• Any other environmental regulations
• Cost of the land or building
The last step of pre-planning involves building a more solid business plan. For this, we need to better understand the farm’s financials and internal systems. This brings us to Step #4: Economic Analysis & Systems Selection.
This stage involves developing an economic model that reflects farm performance, incorporating information that you have compiled from the previous stages along with internal systems you want in your farm. A comprehensive economic analysis should account for: Capital costs, Operational costs, Revenue, Unit cost for all products grown, ROI, Payback period, Labor model, and Wastage scenarios.
Planning your farm also involves having the knowledge of and choosing the right equipment for your farm’s unique needs. According to respondents of the 2020 Global CEA Census, when asked about their initial business decisions, 73% of founders said that they would choose their equipment, technology, or crops differently if they could go back in time. This highlights why working with a highly knowledgeable expert from the early stages of your planning process can be critical.
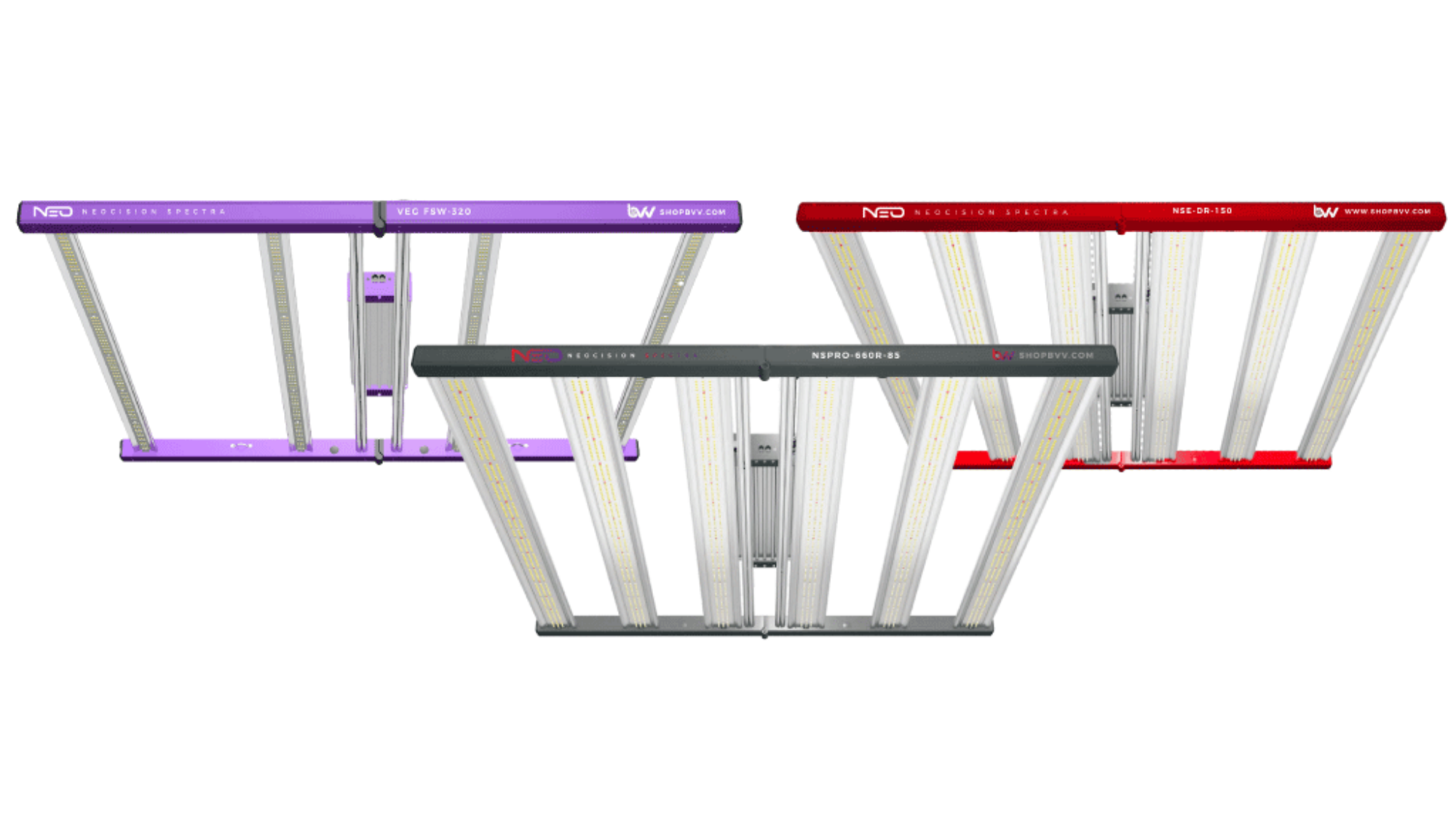
Lighting Systems
It is important to begin lighting selection early on in the facility design process, as it will influence architectural, HVAC, mechanical, electrical, and life safety design coordination. Commercial grow lights vary in cost, output, light spectrums, quality, and energy consumption, so choosing the right lighting for a CEA operation is essential for proper plant growth.
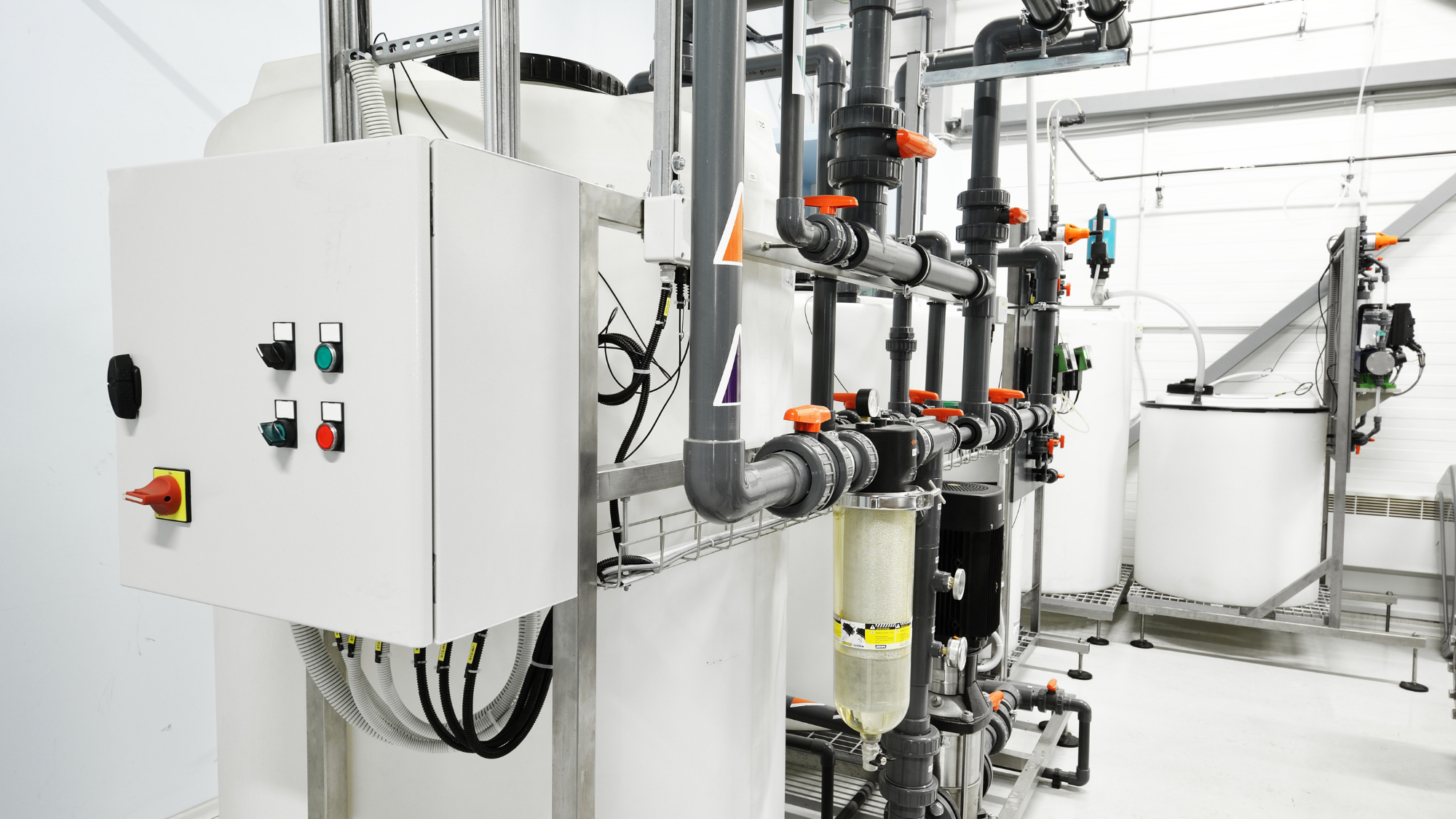
Water Systems
CEA operations have several water management systems. Purification allows an operation to remove particulates, pathogens, and debris for a consistently clean supply of water. CEA operations are typically more efficient when they incorporate an irrigation system into the facility design. Fertigation is the process of automating the injection of nutrients into the water supply, helping to keep the recipe consistent.
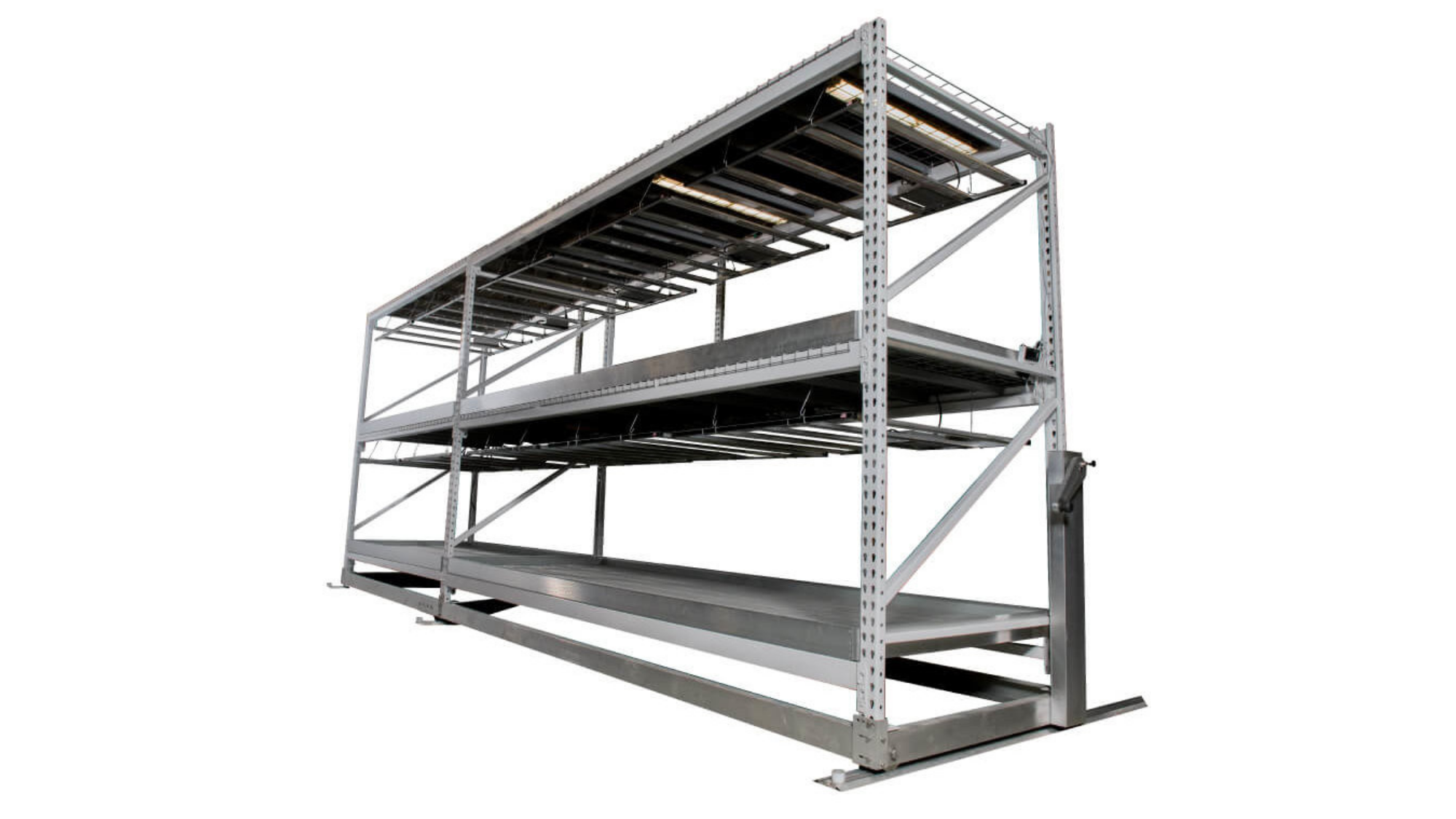
Benching & Racking Systems
Grow benches and racking systems are necessary for efficiently organizing plants within a grow space. There are many benching and racking options available on the market, including stationary benches and racking, rolling benches, track benches and multi-tier racks, and cloning and drying racks.
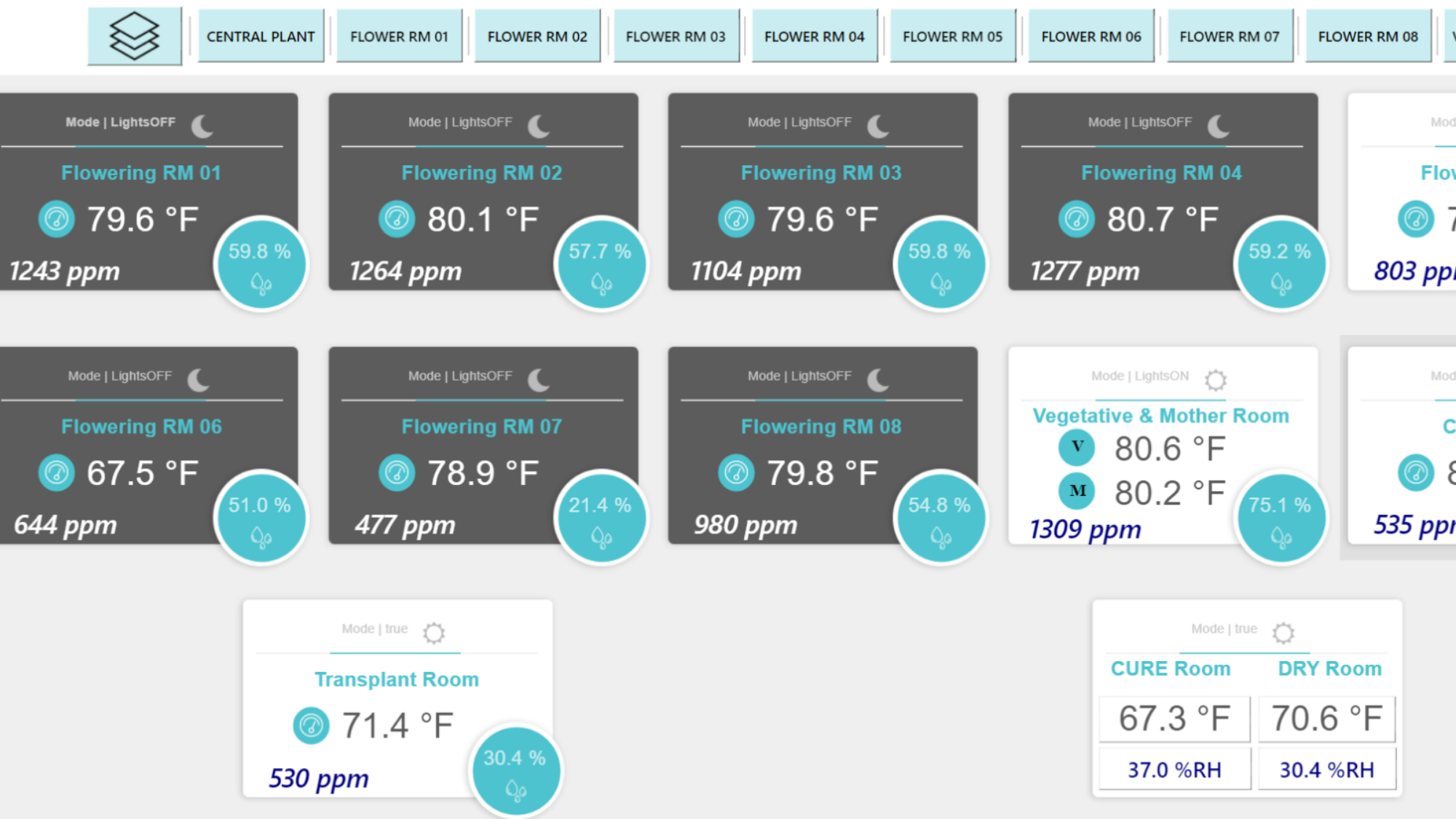
Controls, Data Collection, and Automation Solutions
From irrigation to lighting to HVAC and all of the systems in between, you need controls. Variances in the sophistication of the systems and how they will be operated will determine the level of sophistication required by the controls in the facility. During the early planning of the facility, it is important to determine what the goals are for this precise reason.
With this step complete, you now have a solid business plan in place. It’s time to begin planning the facility, commissioning designs, submitting permits, and breaking ground on the actual build. The more attention to detail you spend on these planning steps, the more time and money you save your business later.
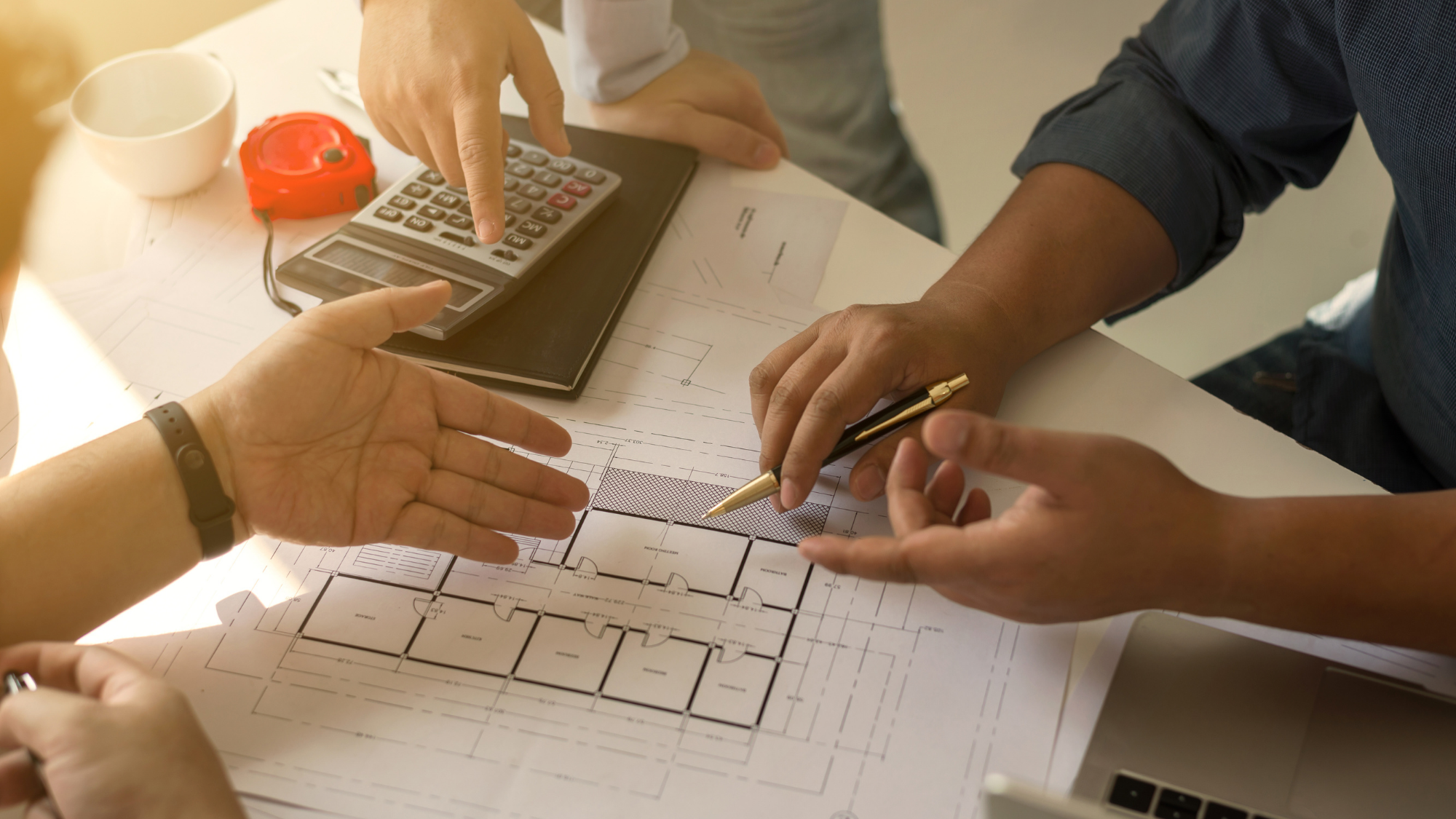
#5: Identifying Professionals for Architectural Design and Floor Plans
Crop needs clearly differ from human needs. As such, it is important to seek out architects and firms that have experience in designing indoor cultivation facilities. Choosing the wrong architect could lead to costly construction delays or risk the entrepreneur getting stuck with an expensive facility that does not meet operational needs.
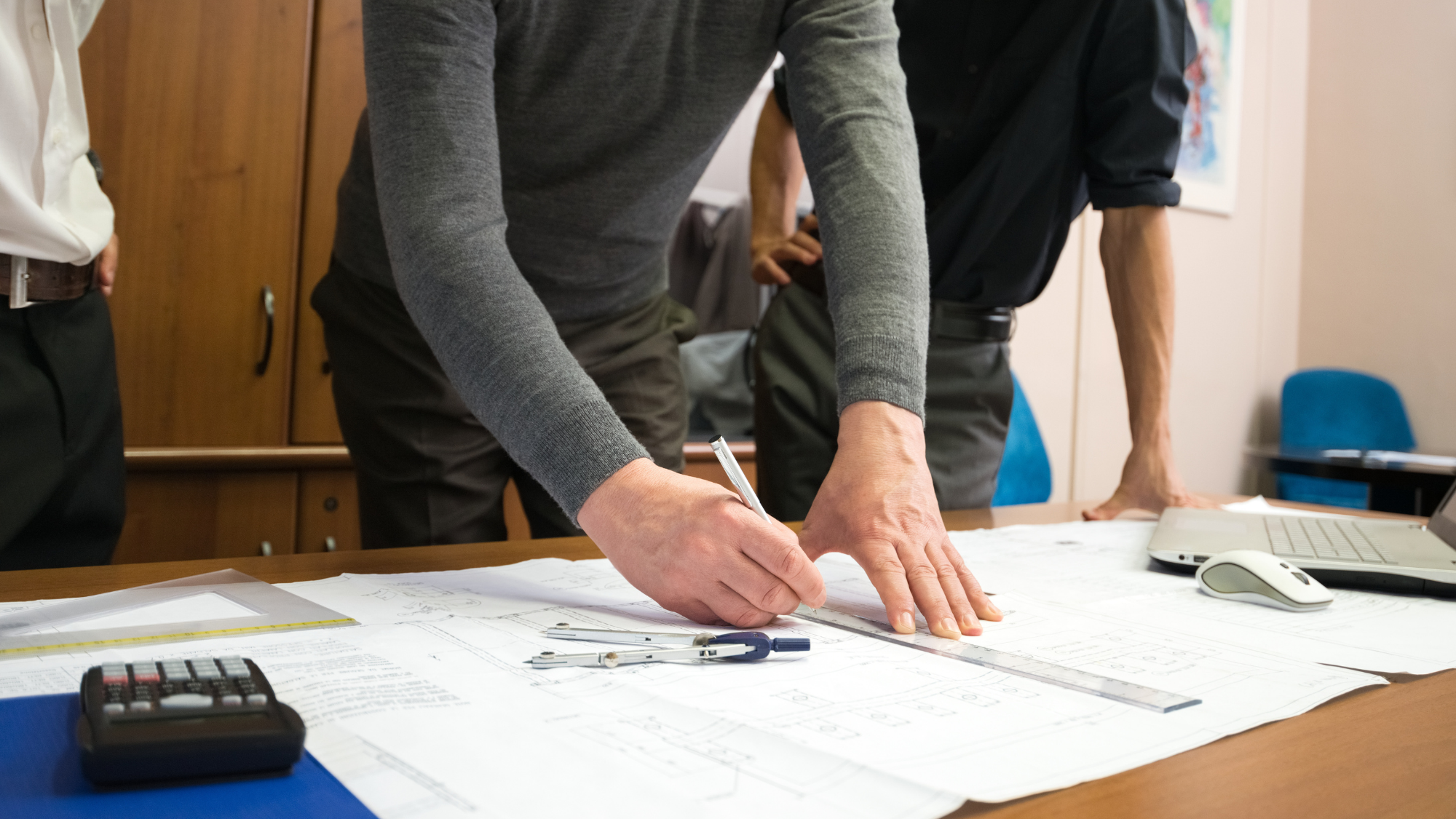
#6: Mechanical, Electrical, and Plumbing (MEP) Design
Professional engineers provide tailored solutions that are designed specifically for the facility’s unique requirements. The right engineering team will offer a wide range of design flexibility, rather than trying to force fit a single option. The MEP’s design the nuts and bolts of the facility; how you will heat cool and dehumidify or humidify the cultivation spaces, the electrical systems and the plumbing systems ensuring proper handling of fresh and wastewater.
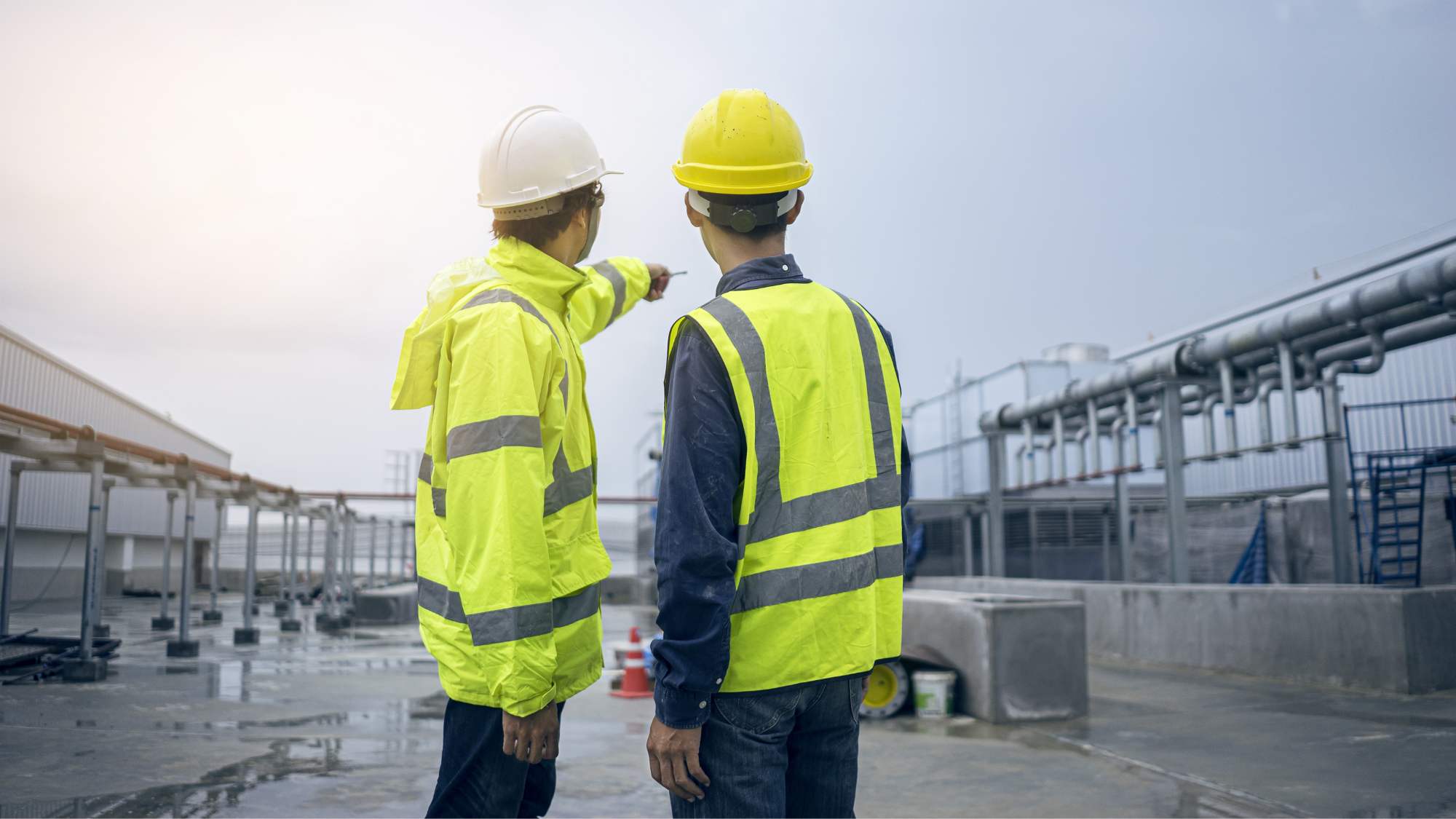
#7: Mechanical, Electrical, and Plumbing (MEP) Permits
In addition to general building permits issued against architectural design drawings, MEP permits must also be issued for construction to begin in most municipalities. MEP engineers provide a number of services needed to prepare an indoor farm for operation, so it is critical to involve an experienced engineering team as soon as possible in the planning process.
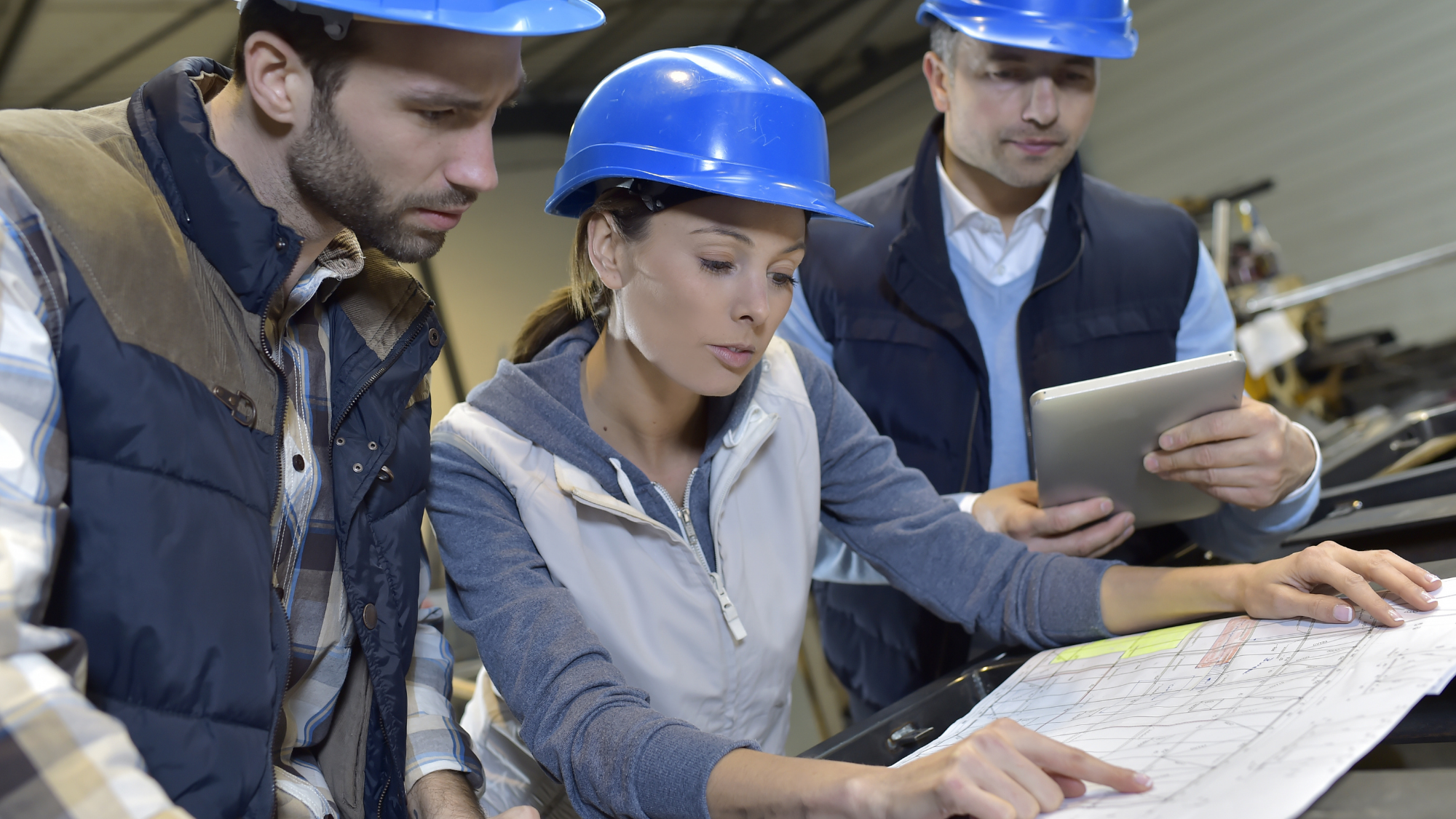
#8: Coordination and Project Management
In farming, everything is connected; every design and equipment decision will affect something else in the facility’s design. For instance, decisions around lighting and racking will have a direct impact on HVAC alongside the architectural and electrical components of the facility. As such, it’s critical that the design team be well-coordinated, with a central point of responsibility directing traffic.
Managing these teams and your time can be a hassle whether you’re new to food production or you’ve had your hand in the industry for a while. Having one partner with expertise in all four of these stages can save you a lot of time and energy.
Surna’s full suite of services has your back. Their architectural and engineering teams work together to ensure efficiencies throughout the planning process so that you can have healthier crops, improved energy efficiency, and superior reliability. With direct cultivation expertise, particularly in climate control solutions that attend to the unique needs of the plant, Surna is able to design a superior facility for both your crops and your employees while considering the entire operation.
And that brings us to Step #9: Equipment Commissioning.
It is time for system commissioning once a CEA operation has been outfitted. This step is critical for ensuring that each system is fully operational. Some systems will need to be commissioned in parallel, and some may be dependent on others. Surna Cultivation Technologies provides system start-up and testing support for the HVAC and controls systems that they provide. During this process, they send out their own field technicians to the facility site to ensure that everything is running as intended, assisting operators with a smooth startup.
Plants require environments designed for agriculture, so it is critical to choose vendor partners who are experienced in CEA during each stage of the facility design process. This applies to consultants, engineers, architects, lawyers, real estate agents, general contractors, lighting companies, HVAC equipment manufacturers, and everyone in between.