Sep 11, 2017
SEPTEMBER SPOTLIGHT: LIGHT POLYMERS’ GROWBLADE™ FLAT PANEL LIGHTS FOR VERTICAL FARMING
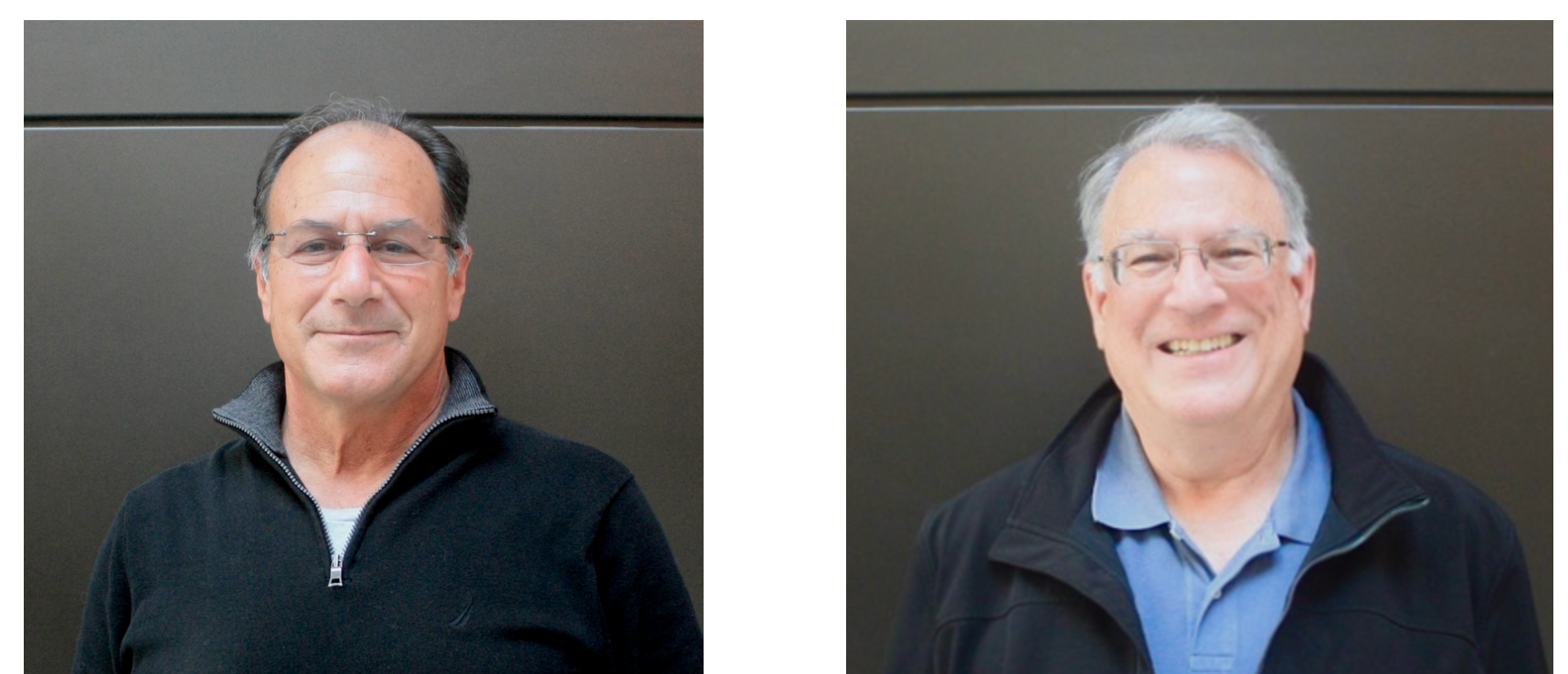
Light Polymers is the newest horticultural LED grow light maker on the market, but at Agritecture we’ve been tracking their innovation since we first met nearly one year ago at a LARTA Institute event in Los Angeles.
After closing a multi-million dollar strategic funding deal, Light Polymers is now announcing its first GrowBlade™ flat-panel LED grow lights, designed for vertical farming and other controlled environment applications. We’re excited to introduce them as Agritecture’s featured Sponsor for September and to highlight their new GrowBlade lights in the +Farm demo at our offices during NYC AgTech Week. We interviewed Sandor Schoichet, VP of Grow Products at Light Polymers, to learn more.

First GrowBlade prototype made from an Altoids Mints tin
Agritecture: Let’s jump right in. What is your team’s background and how did you come together to develop the GrowBlade system?
Sandor: The Grow Products story started almost two years ago when I met Marc McConnaughey, CEO of Light Polymers. We were both part of the Bay Area Alliance of CEOs, a sort of mutual support organization for business leaders. Marc gave a talk where he demonstrated how their Crystallin® photonic film could down-convert blue LED light into beautiful high-CRI (Color Rendering Index) white light. I had recently read The Vertical Farm by Prof. Dickson Despommier and was thinking about opportunities to build a business related to indoor farming. So I asked Marc if his team could formulate a PAR (Photosynthetically Active Radiation) spectrum film. The challenge caught the interest of Dr. Evgeny Morozov, Lead Materials Scientist at Light Polymers, and shortly thereafter we had a lab bench prototype made from a hand-coated film sample and an empty Altoids mints tin. It was destiny calling and we haven’t looked back since!
A: Tell us a bit about Light Polymers’ history.
S: Light Polymers is a nanochemistry company with deep domain knowledge of lyotropic materials, which have a wide range of uses in addition to LED lighting, including LCD and OLED flat panel displays, biomedical assays, and advanced building materials. Light Polymers was started in 2013 in San Francisco and our OLED chemistry is now in trial stages with potential commercialization partners in the display industry. Our Crystallin family of LED downlights was launched in select Asian markets in August. The GrowBlade family of flat-panel grow lights that we’re announcing later this month at NYC AgTech Week will be our first step into the commercial horticulture lighting business.

Sandor Schoichet inspecting the Isabel alpha-test site
A: What do you think an entrepreneur or buyer should look for in horticultural LED lights?
S: Both products and vendor services that help growers achieve their operational and financial goals. At Light Polymers, we’re not focused only on high-quality lighting; we’re developing a family of over-canopy lighting and sensing products designed to integrate with farm management software. Delivering robust and profitable growing systems for indoor vertical farming is a challenge that the industry is still learning to meet. We intend to be part of the solution that lets vertical farming and controlled environment agriculture (CEA) scale into the global food supply sector.
A: How will Light Polymers continue to stay on the cutting edge?
S: There are three different ways we want to push the envelope. First is building a solutions-oriented business culture, delivering high-performance lighting systems. As the industry continues to grow there will be many opportunities for a responsive team to partner with innovative customers. In support of the solutions strategy, our second focus is building real depth in the science of photobiology, in installation design and engineering, and in farm management systems integration. Our third front reflects our team’s experience with virtual production models that leverage the high-volume flat panel lighting and display supply chain. This experience will allow us to be very aggressive on pricing and delivery for our customers.

GrowBlade Edge 1400 panels at Isabel (alpha-test samples)
A: What excites you about vertical farming?
S: I’ve always been interested in the way that technology and society co-evolve. Over the past several years, studying the sustainability of our society and its infrastructure has become a passion. These three themes, technological innovation, social change, and the need for sustainability, are now coming together in a generational wave of change that will impact agriculture and the entire food supply sector. Controlled environment agriculture is a vital part of responding to macro trends like population and economic growth, urbanization, water scarcity, agricultural runoff, climate change, and food security.
As a designer, an engineer, and a developer, helping address a part of this challenge is very exciting. Indoor CEA is just starting to come together as a serious industry sector, and there is huge scope for creative product and service developments. We’ve placed early alpha-test lights with several organizations, including the MIT OpenAg Initiative. The work they’re doing with the open source Food Computer reminds me so much of the early days of distributed computing workstations and homebrew computer clubs, and we know how that scaled beyond all expectation. I’ve worked in a number of different areas over my career, including digital engineering, networking, biotech and business development. Developing our lighting business for vertical farming lets me combine elements of them all.

GrowBlade Edge 1400 panels at Isabel (alpha-test samples)
A: What makes Light Polymers’ GrowBlade product line stand out?
S: Our GrowBlade flat panel grow lights deliver even, wide-area, fully diffused illumination, without hot or cold spots, and will be available in a range of tailored PAR spectra. The whole GrowBlade product family is designed to allow farmers to grow closer, increasing productivity within a given footprint, while improving crop consistency and quality.
What makes our flat panel lights possible is a new generation of remote photonic down-conversion films, based on our proprietary Crystallin® lyotropic coating and suspension chemistry. Remote down-conversion is not a new concept to the LED industry, but implementation and cost issues have kept it from being widely adopted despite its many advantages. Current down-conversion films are made from a silicon resin, using toxic chemistry in a time-consuming, low yield process. They’ve been limited to niche applications where high-quality lighting is required, like museums or photography studios. By contrast, our Crystallin chemistry uses water as a solvent and can be coated on roll-to-roll machines with high yield and low cost. The self-aligning properties of the lyotropic material pack the phosphor particles in a dense layer, maximizing blue light conversion and allowing us to lower both production and operating costs.

Stop by Agritecture during NYC AgTech Week to meet Sandor and see the lights in person.
Since the output spectrum is generated by the Crystallin film, we can formulate a wide variety of application-specific spectra tailored for leafy greens and herbs, clones, seedlings and grafts, tissue culture, and greenhouse daylight supplementation. In moving crop systems we can tailor spectra for different stages of the lifecycle. We’re also glad to formulate custom spectra on request.
Other stand-out elements of our solution that will be coming along soon include GrowBlade Hub and Sensor modules. GrowBlade Hubs will simplify power wiring for large installations and transform the individual fixtures into a connected IoT (Internet of Things) platform for active light control, environmental sensing, and crop monitoring. Can’t wait until I’m free to talk about that in more depth!
A: Why did you choose NYC AgTech Week as the first place to show your products to the world?
S: The awesome combination of the Agritecture network, being part of Blue Planet’s +Farm demonstration and a week-long opportunity to meet and talk with a wide range of growers and innovators across the industry made it the obvious choice.
A: Last question, what makes you happy?
S: Designing and building cool things that work. Contributing to the evolution of a socially meaningful new industry sector. Meeting new friends who are making a positive difference in the world. Oh, and sailing!

GrowBlade Edge 600 at Agritecture’s Brooklyn Office (alpha-test sample)